How do brushless DC motors work? The need for a drive circuit explained
-
Automation
-
Health & wellness
-
Life environment
-
Automotive
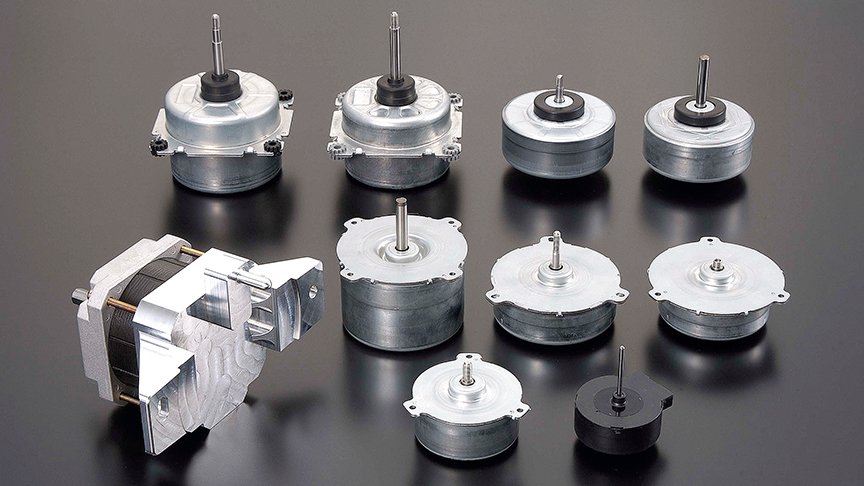
Mar. 24, 2021
DC motors are electric motors that are powered by direct current. Features include the ability to rotate at high speeds, and high starting torque. They are used in a wide range of situations, being a type of motor that is commonly found in numerous familiar applications. DC motors can be broadly divided into two groups: brushed DC motors and brushless DC motors.
This page goes into detail about how brushless DC motors work.
Brushless DC motors offer long life and ease of maintenance
Electric motors can be divided into a number of different types according to their characteristics, such as AC motors, stepper motors, and DC motors. Compared to the other types, DC motors benefit from high starting torque and the ability to rotate at high speeds. They do not suffer from the issues of slip or loss of synchronization.
DC motors can be further divided into brushed DC motors and brushless DC motors, depending on whether they have brushes (electrodes).
- Brushed DC motors
- These motors work by means of the mechanical linkage between their commutator and brushes. The brushes and commutator are in continual contact as the motor rotates. This causes wear of the motors by long-term use that can ultimately result in motor failure. For this reason, brushed DC motors have a shorter life than brushless DC motors, and require regular maintenance. Another disadvantage is the electrical and acoustic noise caused by the continual contact between the brushes and commutator as the motor rotates.
- Brushless DC motors
-
Instead of brushes and a commutator, these motors use electronic means (a drive circuit) to rotate the motor. Having no brushes and commutator, which are both consumable parts, gives the motors a long life and makes maintenance easier. Another advantage is quiet operation as they do not suffer from the noise generated by the contact between brushes and commutator.
How brushless DC motors work: Why is a drive circuit required?
Making an electric motor rotate requires that the direction of current flow through the motor windings (coils) is alternated in order to generate a rotating magnetic field. In the case of brushed DC motors, this is achieved through the mechanical action of brushes and commutator. Then how do brushless DC motors, which don’t have these parts, generate the rotating magnetic field and turn?
Instead of a commutator and brushes, brushless DC motors use semiconductor switches. Brushless DC motors generally have three coils, with semiconductor switches connected to each of these. Turning the semiconductor switches on and off in the correct sequence alternates the current flow, which generates the rotating magnetic field that causes the motor to turn. Accordingly, the motors require a drive circuit to perform this sequencing. Furthermore, the semiconductor switches are switched by detecting the orientation of the permanent magnet rotor, using a magnetic sensor (typically a hall sensor).
Excitation sequence of brushless DC motor
The following link provides more details about the mechanism and control of brushless DC motors.
Do brushless DC motors require a drive circuit? - Controlling brushless DC motors
Outer-rotor and inner-rotor motors
Brushless DC motors can be broadly divided into outer-rotor and inner-rotor motors.
- Outer-rotor motors
- These motors have the coils on the inside and the magnets on the outside, so that it is the outer circumference of the motor that rotates. Although this configuration means that the moment of inertia of the rotor is high, it helps maintain steady rotation.
- Inner-rotor motors
-
These motors have their magnets on the inside as the rotor, and the coils on the outside as the stator. The advantage of this internal rotor configuration is that the rotor has a low moment of inertia, allowing for precise control.
Surface permanent magnet (SPM) and interior permanent magnet (IPM) motors
Brushless DC motors are further divided into SPM and IPM motors depending on how the permanent magnets are attached to the rotor.
- Surface permanent magnet (SPM) motors
- The permanent magnets are attached to the outer circumference of the rotor.
- Interior permanent magnet (IPM) motors
-
The permanent magnets are embedded in the interior of the rotor.
Understanding how brushless DC motors work when using them
Brushless DC motors are electric motors that do not require the consumable brushes and commutator. They benefit from quiet operation together with long life and low maintenance.
Instead of brushes and a commutator, driving a brushless DC motor is done electronically using a drive circuit. The drive circuit is needed to turn semiconductor switches on and off in the correct sequence to generate the rotating magnetic field that causes the motor to turn.
We hope that the information provided here will prove useful to you.
Overcoming your problems with brushless DC motors
ASPINA supplies not only standalone brushless DC motors, but also system products that incorporate drive and control systems as well as mechanical design. These are backed by comprehensive support that extends from prototyping to commercial production and after-sales service.
ASPINA can offer solutions that are tailored to suit the functions and performance demanded by a diverse range of industries, applications, and customer products, as well as your particular production arrangements.
ASPINA supports not only customers who already know their requirements or specifications, but also those who are facing problems at early stages of development.
Do you struggle with the following concerns?
- Motor selection
-
- Don't have detailed specifications or design drawings yet, but need advice on motors?
- Don't have anyone in-house with expertise in motors and can't identify what sort of motor will work best for your new product?
- Motor and associated component development
-
- Want to focus your resources on core technology, and outsource drive systems and motor development?
- Want to save the time and effort of redesigning existing mechanical components when replacing your motor?
- Unique requirement
-
- Need a custom motor for your product, but been declined from your usual vendor?
- Can't find a motor that gives you the control you require, and about to give up hope?
Seeking answers to these problems? Contact ASPINA, we’re here to help.
List of the same series columns
- Applications for blower motor
- What is a blower motor?
- Advantages of brushless DC motors over brushed DC motors
- Features and applications of DC motors
- Is this brushless motor cheap or expensive? - What factors determine its price?
- Different types of DC motor and their respective features
- What is a geared brushless DC motor?
- How does an electronic speed controller for a brushless DC motor work? And what should you consider when you choose the right one?
- Small brushless motors
- Difference between brushed motor and brushless motor
- What are the disadvantages of brushless DC motors? And how can they be overcome?
- Advantages of brushless DC motors: How they differ from brushed DC motors
- What is a stepper motor?
- What is an actuator?
- What is an electric motor?
- What is a brushless DC motor?
- Do brushless DC motors require a drive circuit? – Controlling brushless DC motors
- How do brushed DC motors work? The need for regular maintenance explained
- How are stepper motors controlled? - Speed control of stepper motors
- How are DC motors controlled? - Speed control of DC motors
- Brushless DC motor applications: examples that demonstrate their features
- Stepper motor applications: Examples that demonstrate their features
- Motors designed for easy control: How do stepper motors work?
- What are the differences between brushed and brushless DC motors?
- What is a PSC motor
- What is a servo motor?
- What is a blower?
- What is a DC motor? - features and mechanisms
Contact us for more information
- New inquiry
- Prototype
- Upgrade
- Customization
- Your spec
- Literature
- Support
- Others