Do brushless DC motors require a drive circuit? – Controlling brushless DC motors
-
Automation
-
Health & wellness
-
Life environment
-
Automotive
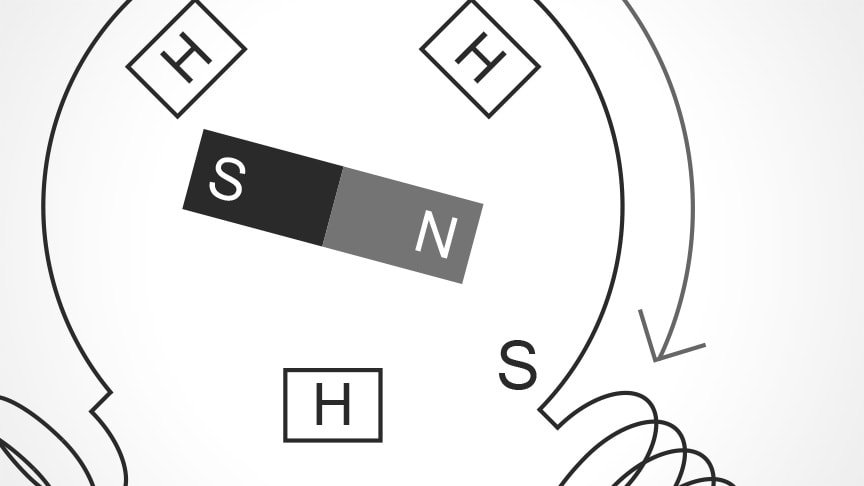
Feb. 24, 2021
As their name suggests, brushless DC motors do not have brushes. They are used in a wide variety of applications, featuring longer life and quieter operation than brushed DC motors.
However, rather than mechanical control, electronic control is needed to drive brushless DC motors. So, how is this accomplished? This page provides a simple introduction on how brushless DC motors are controlled.
What is a brushless DC motor?
Brushless DC motors are DC motors that do not require the brushes used in conventional brushed DC motors.
Brushless DC motors have the following two major advantages over brushed DC motors.
- Long life and therefore low frequency of maintenance
- Quiet operation
The brushes used in brushed DC motors are in continual contact with the commutator. As motor rotation causes the brushes and commutator to wear over time, they need to be replaced regularly. The associated short life and requirement for maintenance is a disadvantage of this type of electric motor. Because brushless DC motors, in contrast, do not use these consumable commutator and brushes, they have longer life, and maintenance is much less frequent. As a result, brushless DC motors have come to be used more frequently.
The fact that brushless DC motors do not use a commutator and brushes also means that the electrical and acoustic noise caused by contact between these parts are eliminated. As a result, brushless DC motors operate very quietly.
Where are brushless DC motors used?
Brushless DC motors are used in a wide variety of applications that take advantage of their quiet operation, long life and low frequency of maintenance. Familiar examples include home appliances such as air conditioners, air cleaners, and refrigerators.
The motors are also found in a wide range of commercial equipment including industrial printers, vending machines, water heaters, and projectors. Together with other applications such as automobiles and large industrial machinery, brushless DC motors have become an essential part of our lives.
Do brushless DC motors require a drive circuit?
As noted above, rather than mechanical control, electronic control is needed to drive brushless DC motors. The reason for this can be explained by how the generation of a rotating magnetic field in brushless DC motors differs from other motors.
In order to make an electric motor rotate, you need to alternate the direction of current that flows through the motor windings, and generate a rotating magnetic field. While induction motors and other motors driven by an AC power supply can use the alternating mains voltage to achieve this, motors driven by direct current require some form of switching to alternate the direction of current flow in the motor, and thereby generate a rotating magnetic field.
In the case of brushed DC motors, this is achieved by using brushes and commutators. With brushless DC motors, however, instead of using brushes that suffer from a short operating life, the alternation of current flow and consequent generation of a rotating magnetic field is achieved by means of semiconductor switches (such as bipolar transistors or FETs), which operating life is not a major concern.
Coil configuration and switching of brushless DC motors
Brushless DC motors generally have three coils. The three coils are connected together at one end, so by connecting the other end of one coil to the positive pole, and that of another coil to the negative pole, causes current to flow through both of these two coils. Two semiconductor switches are connected to each coil, one of which connects to the positive pole and the other to the negative pole. This gives a total of six switches, which, when turned on and off in the correct sequence, causes the motor to rotate. The timing of this switching is determined based on rotor orientation, which is detected by a hall sensor.
In other words, turning the semiconductor switches on and off in the correct sequence generates the rotating magnetic field that causes the brushless DC motor to rotate. And thus, a drive circuit is needed to perform these sequence of steps.
Excitation sequence of brushless DC motor
Configuration of brushless DC motor drive circuit
Drive circuits are made up of the following main elements.
-
Rotational position sensor
A hall sensor that detects the N and S poles of the rotor magnet.
-
Position detection circuit
A circuit that converts the signal from the hall sensor into a digital logic signal.
-
Logic circuit
Based on the signal from the rotor position detection sensor, this circuit outputs the sequencing that controls the direction of current flow through each coil.
-
Pre-drive circuit
A circuit that converts the sequencing signals into the signals for turning the semiconductor switches on and off.
-
Semiconductor switches
Typically, six semiconductor switches are used. These are turned on and off in accordance with the sequencing signals to achieve the current flow through the coils needed to make the motor rotate.
-
Motor drive power supply
Power supplies are required to provide the current flow through the motor coils and to power the logic and sensor circuits.
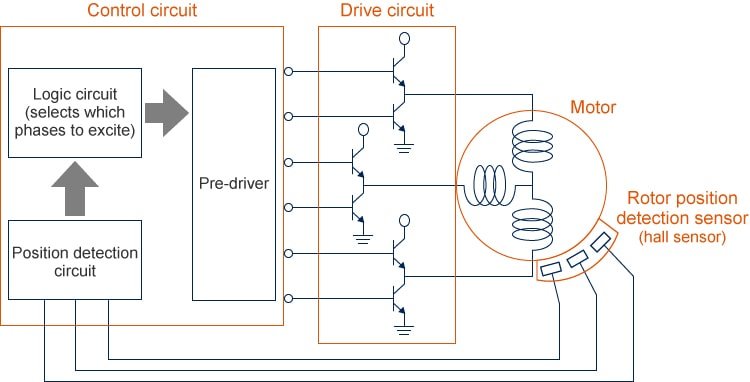
In this way, although they require a drive circuit, brushless DC motors have high performance as they do not have the problems of noise and short life that are an issue with brushed DC motors.
Gaining a deeper understanding of how brushless DC motors are controlled
Because they do not use a commutator and brushes, driving a brushless DC motor requires electronic control rather than using a mechanical mechanism, and this is done using a drive circuit. The drive circuit is made up of a rotational position sensor, position detection circuit, logic circuit, pre-driver circuit, semiconductor switches, and a motor drive power supply. Anyone engaged in building electronic devices that incorporate brushless DC motors need a deep understanding of the role of each element. We hope that the information provided here will prove helpful.
Overcoming your problems with brushless DC motors
ASPINA supplies not only standalone brushless DC motors, but also system products that incorporate drive and control systems as well as mechanical design. These are backed by comprehensive support that extends from prototyping to commercial production and after-sales service.
ASPINA can offer solutions that are tailored to suit the functions and performance demanded by a diverse range of industries, applications, and customer products, as well as your particular production arrangements.
ASPINA supports not only customers who already know their requirements or specifications, but also those who are facing problems at early stages of development.
Do you struggle with the following concerns?
- Motor selection
-
- Don't have detailed specifications or design drawings yet, but need advice on motors?
- Don't have anyone in-house with expertise in motors and can't identify what sort of motor will work best for your new product?
- Motor and associated component development
-
- Want to focus your resources on core technology, and outsource drive systems and motor development?
- Want to save the time and effort of redesigning existing mechanical components when replacing your motor?
- Unique requirement
-
- Need a custom motor for your product, but been declined from your usual vendor?
- Can't find a motor that gives you the control you require, and about to give up hope?
Seeking answers to these problems? Contact ASPINA, we’re here to help.
List of the same series columns
- Applications for blower motor
- What is a blower motor?
- Advantages of brushless DC motors over brushed DC motors
- Features and applications of DC motors
- Is this brushless motor cheap or expensive? - What factors determine its price?
- Different types of DC motor and their respective features
- What is a geared brushless DC motor?
- How does an electronic speed controller for a brushless DC motor work? And what should you consider when you choose the right one?
- Small brushless motors
- Difference between brushed motor and brushless motor
- What are the disadvantages of brushless DC motors? And how can they be overcome?
- Advantages of brushless DC motors: How they differ from brushed DC motors
- What is a stepper motor?
- What is an actuator?
- How do brushless DC motors work? The need for a drive circuit explained
- What is an electric motor?
- What is a brushless DC motor?
- How do brushed DC motors work? The need for regular maintenance explained
- How are stepper motors controlled? - Speed control of stepper motors
- How are DC motors controlled? - Speed control of DC motors
- Brushless DC motor applications: examples that demonstrate their features
- Stepper motor applications: Examples that demonstrate their features
- Motors designed for easy control: How do stepper motors work?
- What are the differences between brushed and brushless DC motors?
- What is a PSC motor
- What is a servo motor?
- What is a blower?
- What is a DC motor? - features and mechanisms
Contact us for more information
- New inquiry
- Prototype
- Upgrade
- Customization
- Your spec
- Literature
- Support
- Others