Leveraging cross-industry success: The advantage of ASPINA's medical ODM
-
Health & wellness
-
CPAP
-
Ventilator
-
Portable oxygen concentrator
-
Cough assistant
-
Syringe pump
-
Peristaltic pump
-
Micro and insulin pump
-
Rehabilitation
-
Prosthesis
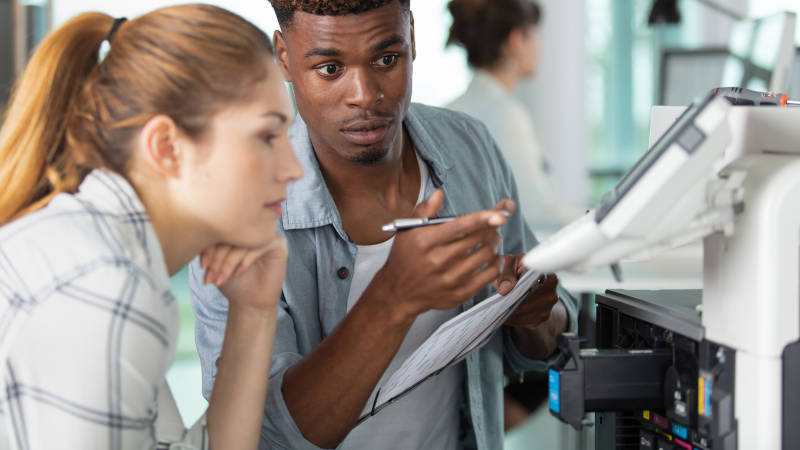
D Corporation: Office document solutions manufacturer
A performance challenge found in the mass production design stage
ASPINA's Original Design Manufacturing (ODM) service for medical equipment is highly reliable and capable, with extensive development experience across various industries. This article highlights a case study on the mechanical design and manufacturing of a module integrated into a long-standing successful product of one of ASPINA’s customers.
D Corporation, a leader in the commercial printer market known for high printing quality, faced a challenge with its new Multifunction Printer (MFP), surpassing previous models and further differentiating itself from competitors. Despite a successful conceptualization phase, D Corporation faced numerous challenges in gearing up for mass production.
MFPs utilize four photosensitive drums, synchronously driven to transfer toner onto copy paper. These drums incorporate the three primary colors (CMY) and black (K), and consistent rotation speeds of these drums are crucial to achieving uniform and high-quality prints. The precision in synchronizing these rotation speeds directly influences the quality of prints. D Corporation aimed to enhance the precision of drum synchronization in pursuit of industry-leading print quality. Unfortunately, the prototype developed for mass production by D Corporation did not meet their expectations in this regard. Identifying inconsistent drum rotation as the root cause, D Corporation found resolving this issue challenging despite their efforts.
Image example of drive module for photosensitive drums. Two motors and worm gears rotate 4 drums.
Resource dilemmas and budgetary battles
Initially, D Corporation had planned to handle the mass production design for the current project in-house. However, they faced struggles due to limited design resources in seeking solutions for the inconsistent rotation issue. The design department of D Corporation was actively engaged in various new product development projects, with engineers working on multiple assignments. Consequently, prioritizing resources for the mass production design of this project became a challenge despite the urgent need for progress.
Furthermore, meeting the targeted cost outlined in the product plan was crucial for D Corporation. They were not only concerned with the cost of purchasing components but also aimed to control human resources in mass production. This included efforts to reduce labor cost in the production line and indirect costs such as human resources in the purchasing process. To achieve cost reduction, D Corporation wanted to outsource assembled units containing motors and gears that rotate the drums.
To maintain its commitment to launching high-quality products quickly and staying ahead of the competition, D Corporation sought to swiftly address challenges and move towards mass production. Finally, D Corporation began searching for a partner capable of handling the entire process from mass production design to manufacturing. With prior success in delivering assembled products in similar projects, D Corporation approached ASPINA.
ASPINA's ODM: Resolving performance, design resources, and cost challenges
At ASPINA, we formed a team of mechanical engineers who possess extensive experience in the design of assembly parts for mass production. We began the project after receiving design drawings from D Corporation. Tetsuo Kayama, Deputy General Manager of the Medical Engineering Business Unit, was involved in this project at that time. He remarked, "We had many engineers who were capable of mechanical design customized for manufacturing processes and were well-versed in mass production techniques."
Our primary focus was on improving the motor rotor axis shaft runout and eliminating gear pitch deviation. To achieve this, we enhanced the accuracy of dimensions, shapes, and positions for each component of the unit.
We specifically revisited the material and structure of the chassis. The original design by D Corporation included welding three sheet metal-formed parts which proved to be insufficient in rigidity, leading to vibrations and shaft runouts under gear load. To address this, we opted for aluminum die-casting as it offers greater design flexibility and thickness, ensuring rigidity. Additionally, we replaced welding with screw fastening to enhance assembly accuracy, as welding often causes alignment errors leading to shaft runout.
We also worked on improving the precision of the worm gear. Synchronizing four photosensitive drums to drive seamless printing required pitch accuracy of the worm that rotates the drums’ worm wheels. The required precision level was stringent, with micro-level errors in single-tooth pitch meshing required to be in the single-digit micron range. Leveraging our capability to perform thread grinding with such precision, we ensured the necessary accuracy. Specifications for the worm grinding process were determined meticulously through close collaboration with D Corporation, responsible for the worm wheels.
We also implemented measures for mass production to ensure assembly precision. Firstly, we applied part machining to place the parts in the correct positions. Secondly, we introduced special inspection equipment for the assembly line. The equipment allowed us to measure the worm’s rotational variation after assembly, carry out frequency analysis, and check for any frequency indicating rotational irregularities.
ASPINA ODM service develops various type of modules and units
ASPINA’s medical ODM supports at any design stages
D Corporation finally launched this new MFP which was developed in collaboration with ASPINA. The MFP’s high image quality drove sales growth, and it became a long-standing product for D Corporation.
While ASPINA was involved in this project from the mass production design process, we have been engaged in other projects from the early stages of conceptualization. According to Kayama, "In those cases, we started without design blueprints. We worked together with customers to solve technical challenges and supported them to finish designing towards the launch of new products."
ASPINA has a rich track record of providing ODM services across various industries, and we have supported customers at any stage of development. Leveraging this expertise, ASPINA also offers ODM services for medical equipment, and we are ready to support businesses as a partner in medical equipment development. If you have any inquiries, please be free to contact ASPINA.
Related information
Customer challenges
- Printing quality issue arose during the mass production design phase, and technical problems that cause the issue remained unresolved.
- With other development projects underway, engineering resources were insufficient to proceed the mass production design of this project.
- Needs to reduce the number of purchased parts and minimize human resources associated with assembly and procurement.
ASPINA solutions
- We reviewed the customer’s design by making changes to the chassis materials and structure, as well as improving the precision of the worm gear.
- We devised components to ensure assembly precision. We also implemented a meticulous measurement of rotational irregularities in the inspection process after assembly.
- We manufactured and supplied units containing motors and gears in-house.
Exhibition information
-
Jul. 9, 2025
-
May 19, 2025
-
Dec. 27, 2024
Related information
Contact us for more information
- New inquiry
- Prototype
- Upgrade
- Customization
- Your spec
- Literature
- Support
- Others