Unprecedented gripping capability made possible by motor technology - robotic gripper
-
Automation
-
Robotics
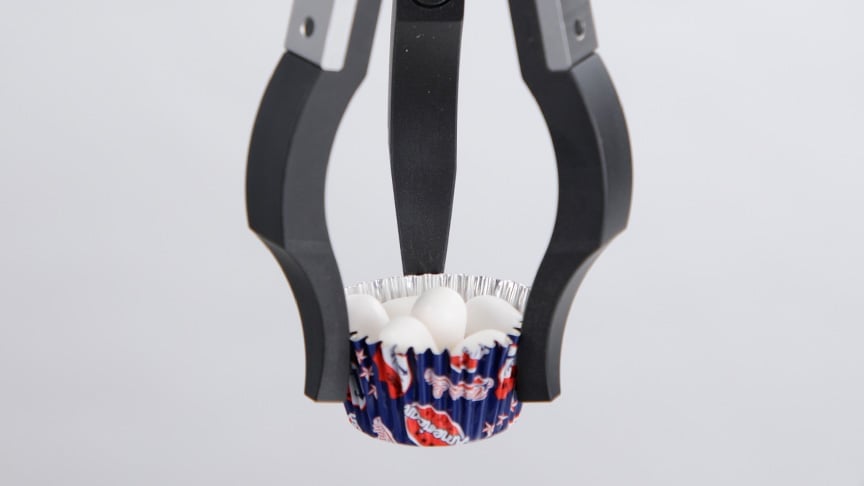
Development of unprecedented electrically driven robotic gripper to overcome labor shortages across numerous industries
"Our motion control technology may be able to help overcome the issues facing society." This was a sentiment shared by everyone attending a product development meeting at the ASPINA Automating Life & Work (AL) Business Unit.
The challenges in question is how to deal with the labor shortages resulting from an aging population and low birthrate. There has been interest from around the world in the use of not only conventional industrial robots but also collaborative robots ("cobots") that work alongside people to help solve this problem. Demand for these cobots is expected to grow around the world, with the 2019 annual report of the International Federation of Robotics (IFR) noting that installation of cobots in 2018 increased by 23% over the previous year to almost 14,000 units.
If cobots are to make up for workforce shortages, they will need to undertake tasks previously only done by humans and one of the biggest challenges is the act of grasping objects that have different sizes, shapes, and hardness. What is needed, then, is a robotic gripper able to grasp a variety of different objects.
Meanwhile, robotic grippers are already in use at manufacturing factories and other sites where they pick up objects with a predetermined shape as part of sequential work. This ability is sufficient for robots to work in such mass production processes. Unfortunately, manufacturing methods are already becoming more diverse with a transition to high-mix low-volume production in which the same production line is used to manufacture a variety of different objects. Furthermore, future use of robots beyond manufacturing will expand demand for robotic grippers that allow the same robot to pick up all sorts of different objects.
"We were confident that the experience and know-how we, an electric motor manufacturer, have built up could bring new ideas in developing a robotic gripper able to pick up different objects." This was how manager of the RT Development Section in the AL Business Unit, Mr. Sasaki, spoke about how they came to the decision to embark on an unprecedented product development, namely an electrically driven robotic gripper able to grasp all sorts of different objects.
Expanding possibilities for robots with all-in-one design capabilities of a motor manufacturer
When considering this requirement of being able to grasp all sorts of different objects, the conclusions were that a long stroke would be needed to deal with objects of different sizes, that a three-finger design would be better at gripping round objects, and a mechanism for rotating the fingers should be included so that they could grasp the object from any direction.
However, an approach of integrating the hand that would do the grasping and the motor that would operate the hand after designing them separately would not give them a robotic gripper that satisfied these requirements while also being small. Deputy Manager of the AL Business Unit, Mr. Nagai, expressed their enthusiasm for applying ASPINA's special mix of product development skills to the task they had set themselves by saying, "We, ASPINA, had the capabilities to undertake an all-in-one design that encompassed the hand, motor, and control unit, and this meant we were able to design a smaller end product by eliminating unnecessary structures and spaces."
Designing the full structure from the motor to the control unit made it possible for us to add new value to the robotic gripper itself. What ASPINA added to their robotic gripper was a "through hole". This is a hole that runs all the way through the electrically driven robotic gripper from front to rear.
A "through hole" runs all the way through the robotic gripper from front to rear
Making the through hole on the robotic gripper expands the potential for automation to incorporate additional operations that can be used when grasping an object. If a camera were fitted through this space, for example, it could be used to view the robotic gripper picking up an object in real time. Potential applications include scanning a QR code on the object for an on-the-spot decision on what to do with it. Other possibilities include fitting an air nozzle to blow dirt off the object or incorporating a vacuum pad to pick up objects more securely.
Exploring internal and external sources for new technologies to meet user requirements
The development objective was finalized as being a small and lightweight electrically driven robotic gripper able to grasp all sorts of different objects and with a hollow space inside. Unfortunately, some major obstacles arose after the actual design work started. The problem was how to build the coupling mechanism between the motor shaft and fingers while still keeping the hand small and light.
Developing such a mechanism from scratch by ASPINA would be costly and time-consuming and this would be an obstacle to developing the product in an efficient and timely manner that was in line with customer budgets and market needs. The solution that the development team came up with was to engage in the collaborative creation of a new cylindrical cam mechanism in partnership with a company that already held a patent for a precision cylindrical cam.
A different department at ASPINA used to work with the company to collaborate on the development of the new cylindrical cam mechanism. We at ASPINA usually have a lot of communication at various levels among teams and departments and it was natural that the information on this company came up in a conversation between the development team and that department, and this is what led to the AL Business Unit entering into the collaboration. We share thoughts, ideas and information beyond the team so that we can accelerate product development and delivery of our products to customers.
Our attitude toward interaction and communication in the company on a daily basis can be seen everywhere, not only in developing and designing products, but also in planning new products and in making product improvements. As Mr. Sasaki explains, "When there is a new product to be developed at ASPINA, staff from different departments come together to undertake the market research to determine customer needs and wants. The ASPINA engineers involved in designing and production engineering do not always sit at their desks, but go outside the company and attend trade shows, seminars, and the like so that they can gather ideas and thoughts in the industry or market concerned as a part of the research. This approach has a great benefit for customers and us because the technical challenges faced by customers and the user's perspective on performance improvement directly come to our engineers, who understand them and actually make things happen with our products."
At robotics trade shows, the engineers had a lot of conversation with visitors from industries where the different shapes and hardnesses of works make it challenging to introduce automation in production processes, and they realized what the actual issues would be for robotic grippers. One example is that ASPINA's robotic gripper has features inspired by a visitor one of our engineers listened to at a trade show saying "how it would be helpful if the fingers could be made replaceable in order to be able to pick up different types of objects". Future plans for making the electrically driven robotic gripper suitable for a wider range of uses include the development of models with different numbers of fingers.
Mr. Nagai also spoke about ASPINA's strengths in market research and product development, saying, "At every stage during product development, we talk directly to customers in this way to figure out what would be market needs and give them as feedback to product development. More so than other vendors, I believe our engineers make frequent visits to customers and have numerous opportunities to participate in meetings with them."
Furthermore, in order to accelerate the delivery to the market of products that customers truly need, ASPINA also proactively sources external expertise and technologies from time to time in its product development.
ASPINA robotic gripper technologies for your need to "grasp everything"
What benefits arise if the electrically driven robotic gripper acquires the ability to grasp objects of many different types? For example, because the objects to be picked up vary from customer to customer, vendors engaged in robot development currently need to design their robotic grippers for each project. Eliminating that design process would reduce the cost of the robots and shorten the lead time until manufacturing. Likewise, it would also eliminate the need for robot users to swap the robotic gripper whenever the object to be grasped changes, simplify work setup, and also avoid the cost of using a tool changer.
Along with continuing to make their electrically driven robotic gripper lighter and more compact, ASPINA also plans to expand the product range to include two-finger models, for example, and to look at ways of replacing the fingers to suit different tasks. While the current robotic gripper is able to grasp objects up to around ten ounces (a few hundred grams), demand for the product would increase further if we make the motor in the robotic gripper more powerful to be able to pick up objects as heavy as around two to four pounds (one or two kilograms). New markets for the electrically driven robotic gripper would likely open up in industries such as food, medicines, and cosmetics where there has been a lack of progress on automation.
We at ASPINA intend to continue supplying custom products that suit customer needs by drawing on our wealth of motor technology, utilizing our product development practices in which the entire company works as one to research fields where there are potential applications for motion control technology.

Exhibition information
-
Jul. 9, 2025
-
May 19, 2025
-
Dec. 27, 2024