ASPINA: The driving force behind the optimal motor selection for revolutionary medical machines
-
Health & wellness
-
CPAP
-
Ventilator
-
Portable oxygen concentrator
-
Cough assistant
-
Syringe pump
-
Peristaltic pump
-
Micro and insulin pump
-
Rehabilitation
-
Prosthesis
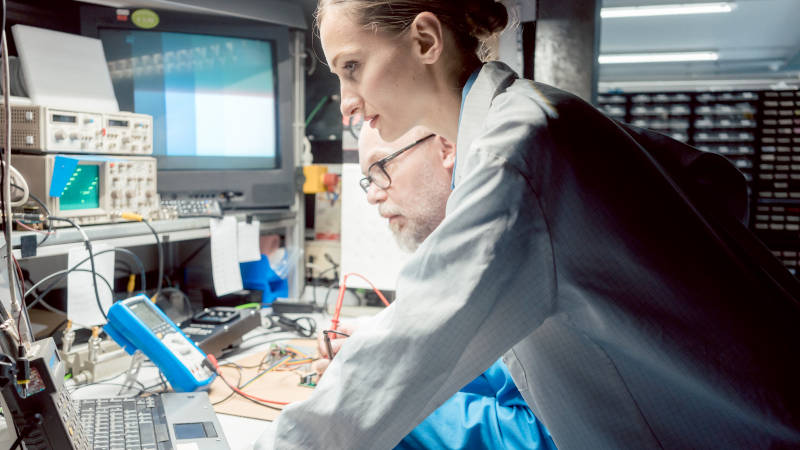
R Corporation: Respiratory care equipment manufacturer
Unraveling motor evaluation complexities in medical equipment development
In this article, we share how our guidance and proposals played a key role in overcoming motor-related challenges during the development of medical equipment by our customer, ultimately expediting the launch of their innovative product.
In the dynamic landscape of respiratory care equipment manufacturing, marked by the drive for market expansion, heightened expectations for improved patient quality of life, and a constant pursuit of technological innovation, M&A activities and business restructuring have become conspicuous trends. Our customer, R Corporation, a leader in this field, has adapted by consolidating development centers offshore and expanding its engineering team. In response to a corporate mandate to for innovation, R Corporation initiated a transformative project for next-generation respiratory care equipment. This compact solution, designed for bedside and in-bed use, represented a significant leap in patient convenience and care.
During the transition from prototype to mass production design, the development team's focus turned to selecting a compact motor for the equipment's compressor. They chose to design the compressor in-house while using a commercially available driver for motor control. After identifying potential motors and setting up an evaluation environment, unexpected challenges arose. Despite the motor's specifications appearing sufficient for the compressor's load, it ceased rotating before reaching the required torque. "We checked factors like power supply, but the root cause remained elusive," an engineer from the development team reported.
In the evaluation of motors, it is crucial to not only understand the motors themselves but also be well-versed in the relationships and evaluation methods concerning factors like load characteristics, motor drive methods, and power supply capacity.
Navigating customization hurdles and cost constraints in motor selection
During the development process, the R Corporation development team encountered significant obstacles related to motor customization and cost concerns, which led to over a year of delays. The challenge began with the realization that the mounting section of the off-the-shelf motor they selected for their next-generation equipment could not be customized making it impractical to fit into the compact enclosure of the machine. Additionally, further complications arose when they needed to connect the motor's shaft to their proprietary compressor. A custom spacer was required, but with no ready-made options available and lacking internal design blueprints, the team was faced with starting the design process from the ground up. Adding to these technical difficulties, the cost of the selected motor was prohibitive, significantly impacting the projected profitability of the product. As these challenges mounted during the mass production design phase, the development team encountered prolonged setbacks.
A breakthrough occurred when the team learned from their procurement department about ASPINA's expertise in supplying custom motors for various applications. Recognizing an opportunity to resolve their dilemmas, they reached out to us for consultation.
Engineering synergy: ASPINA’s approach to proposing a compact and cost-effective motor for medical equipment
The journey to optimal motor selection for R Corporation's innovative medical equipment involved a close collaborative effort with ASPINA. The R Corporation team invited an ASPINA engineer to their development site for hands-on evaluation tests. During these tests, the ASPINA engineer identified an issue with the method used to measure power supplied to the motor. By adopting the correct measurement technique, as advised by ASPINA, the team uncovered that the driver's power setting to prevent overcharging was lower than needed. Adjusting these settings allowed them to accurately calculate the torque necessary to operate their compressor.
To accurately determine the motor's specifications and enable mechanism design within a compact enclosure, the development team lent ASPINA a prototype they had created. Leveraging extensive experience in motor development and manufacturing, ASPINA conducted a comprehensive evaluation. This process utilized their deep expertise in integrating components around motors and insights from their own compressor development efforts.
Tetsuo Kayama, Deputy General Manager of ASPINA's Medical Engineering Business Unit, stated, "Standard motors can often lead to size and cost inefficiencies due to overspecification. In this case, we recognized an opportunity to propose a new design motor tailored for the next-generation respiratory care equipment, balancing torque requirements with size and cost considerations."
With over 50 years of experience in motor development, under Kayama's leadership, the ASPINA’s engineers custom-designed the ideal motor for this application. They chose an outer rotor type brushless DC (BLDC) motor from our lineup, aligning it with the compressor's load characteristics and space limitations. This motor, while not fully custom, included components common in many ASPINA motors for standard products, ensuring compatibility with medical device quality standards and maintaining both reliability and cost-effectiveness. The design also considered ease of assembly for mass production, integrating spacers between the compressor and the motor to streamline integration within the compact enclosure.
ASPINA outer rotor BLDC motors
R Corporation, convinced by ASPINA’s innovative approach, adopted the proposed motor solution, combining it with shafts, spacers, and mounting parts to connect to the compressor. This collaboration resulted in a significantly downsized, yet highly efficient, respiratory care equipment, marking a milestone in medical equipment innovation.
Navigating the complexities of medical equipment approval and component lifecycle management
For medical equipment manufacturers like R Corporation, achieving the right balance between quality management in medical device development and manufacturing, and maintaining product profitability, is paramount. ASPINA plays a critical role in this equilibrium, optimizing the Quality, Cost, and Delivery (QCD) of the components we provide. Our approach is comprehensive, spanning from conceptual design to mass production and ongoing after-sales support. We tailor our quality management strategies to meet our customers' specific needs at each stage of development, including evaluation criteria, production line cleanliness, traceability, and more. "We ASPINA distinguish ourselves among motor manufacturers by possessing an in-depth understanding of the intricate certification processes in medical device development and manufacturing. Our approach is tailored to meet the unique quality management demands of each customer," emphasizes Kayama.
ASPINA’s product development and manufacturing process involves providing and exchanging optimal information and items at each stage of customer medical equipment development and manufacturing.
Beyond the scope of this specific case, a major ongoing challenge for medical equipment companies is managing the End-of-Life (EOL) of components in devices with extended lifecycles. In response to this industry-wide issue, ASPINA offers solutions designed for prolonged supply, effectively addressing these long-term challenges. Our commitment is to be more than a supplier; we aim to be a growth partner for our customers in the medical equipment sector.
ASPINA builds long-term partnerships tailored to the specific circumstances of medical device development and manufacturing, such as approval review periods and product life cycles.
As a partner in medical equipment development, ASPINA helps our customers grow their business. For more information on how ASPINA can support your business needs in the ever-evolving landscape of medical equipment manufacturing, please contact us.
Related information
Customer challenges
- Expertise shortfall in motor selection: Due to M&A, business restructuring, and a prolonged absence of new model development, the development team lacks the expertise to evaluate and select motors effectively.
- Integration challenges with standard motors: Integrating off-the-shelf motors into compact enclosures has proven to be a complex task, leading to increased material costs and design complications.
- Certification process complexities: Finding a motor manufacturer capable of navigating the complex and lengthy certification process required for medical equipment has been a formidable challenge.
ASPINA solutions
- Expert guidance in motor evaluation: ASPINA offers guidance on motor evaluation by actively participating in the development process. We provide hands-on assessment and testing within the actual development environment, using the equipment in question to ensure optimal motor evaluation.
- Customized high-performance motors for compact spaces: We propose motors that not only deliver high performance but are also specifically designed to fit within small enclosures. Our solution includes a tailored mechanism for mounting and a custom spacer to ensure seamless integration.
- Flexible quality management and sustainable supply systems: Recognizing the unique demands of medical equipment development and manufacturing, ASPINA establishes flexible quality management processes and ensures a sustainable long-term supply system to meet customer-specific requirements in medical equipment development and manufacturing at optimal costs.
Exhibition information
-
Jul. 9, 2025
-
May 19, 2025
-
Dec. 27, 2024
Related information
Contact us for more information
- New inquiry
- Prototype
- Upgrade
- Customization
- Your spec
- Literature
- Support
- Others