Carts and robots handle heavy loads with ASPINA In-Wheel motor solution
-
Automation
-
Mobility assist
-
Delivery robot
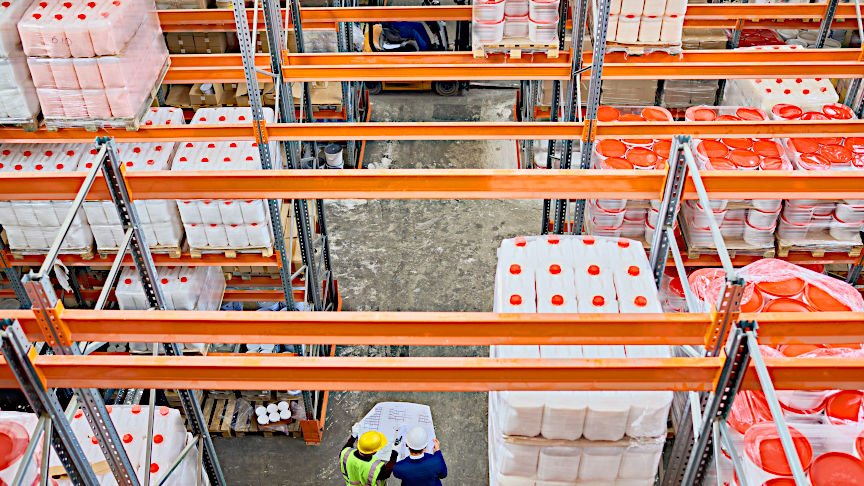
Motorized cart, drivetrain platform, autonomous robot
Motorized carts and autonomous robots that move heavy loads need proper motion control for safe operation
A lot of aspiring engineers are now focusing on product development of motorized carts, drivetrain platforms, and autonomous robots that can move heavy loads or assist people to navigate. When their total weight including the carrying items is heavy, a major development challenge is how to avoid sudden changes of motion for safety operation.
For example, when a cart, platform or robot autonomously moves an object weighing more than 200 pounds (approximately 90 kg), you have to design precise control over large inertia that occurs when starting, stopping, turning and avoiding objects, otherwise it may move quickly and destroy or damage the carrying items and/or the vehicle itself. In addition, there is a high risk of injury from collision with a nearby individual at the workplace or from the sudden and unexpected pushing or pulling force applied to the operator.
Motorized carts, drivetrain platforms, and autonomous robots mainly use wheels, motors, and gears to move electrically. You may purchase those components separately and install them in your products at your factory. In this case, you would have to develop the sensing mechanisms, drive and controlling circuits, and software in order to realize appropriate speed, position and torque control that is made by integrating those components. You would be required to spend much of your time and resources to design and create optimal control. This would include studying motor characteristics such as starting/stopping torque and braking, as well as, the optimal reduction ratio and mechanical design of the motor, gears and wheel. All of this combined is to find the necessary performance of those components with the drive and control circuit board and software.
Motors, gears, shafts, drive and control circuits, software – you would need a lot of development resources to create an optimal control
The size, motion and other factors to consider when you apply In-Wheel motors
Motorized carts, drivetrain platforms, and autonomous robots need to be small enough to work without colliding with walls, pillars, shelves or objects on the floor. However, those vehicles tend to become large and bulky when they mount motors, gears, a drive circuit and a battery in the platform.
An In-Wheel motor, which houses some or all part of the motor and gears inside the wheel, is one of the solutions to make the platform small and reduce the size of the cart or robot you design.
However, some In-Wheel motors have its motor and gears protrude outside the wheel and are larger in size. You may face difficulty when trying to get an In-Wheel motor that fits your product in size. In addition, you also need to think of housing a drive circuit board and a battery in the platform, as well as the wiring to connect them. The transition to In-Wheel motors is not as simple as “replace the caster" approach.
You need to prepare drivers and software for speed control, position control and torque control even if you use In-Wheel motors. It may take many man-hours to understand the characteristics of the In-Wheel motor and to design and create optimal control for its intended use.
ASPINA’s In-Wheel motor solution creates compact, safe carts and robots
We recommend our compact In-Wheel motors for motorized carts, drivetrain platforms or autonomous robots you design. For example, our 200-watt In-Wheel motor, with a wheel outside diameter of 7.9 inches (200 mm) and a width of 5 inches (128 mm), integrates a high-efficiency motor, high-precision reduction gears and an electromagnetic brake. As a motor manufacturer having expertise in designing motors, reducers and electromagnetic brakes for integration, we have designed for the motors and gears to fit into the wheel.
Our contract partners applied ASPINA In-Wheel motors to their new motorized carts to make them as compact in size as their existing manual carts.
We offer more than just an In-Wheel motor. We can develop and supply drive modules and software that control the In-Wheel motors to start, stop, and change the speed of the carts and robots according to the status of their movement with or without manual navigation.
ASPINA 200W type In-Wheel motor integrates a high-efficiency motor, high-precision reduction gears and an electromagnetic brake
In addition, we perform the mechanical design of the In-Wheel motor and the drive module to house them, a battery and other necessary components in the platform.
Our solution of integrated In-Wheel motors, drive and control circuits, and software can reduce the resources of your team to develop motorized carts, drivetrain platforms and autonomous robots.
With sixty years of experience in developing drive systems, ASPINA In-Wheel motors helps you innovate your moving and transporting capabilities
Motorized carts, drivetrain platforms and autonomous robots which employ ASPINA's In-Wheel motors, drive circuits and control software bring the benefit of significantly reducing the workforce to warehouse operators, construction companies and equipment manufacturers.
One of our clients, a maker of motorized carts, estimates that carts that weigh nearly 2,000 pounds (900 kg) could save up to 70% of labor cost if only two people push and guide the cart instead of five to seven.
With nearly sixty years of experience in the development and manufacture of drive systems and motors, we at ASPINA focus on the value each of our customers truly desires to achieve and offer the best solutions with our product line-up including custom models. Our products have met a wide range of customer needs in applications of robotics and automation.
Create your innovative products with ASPINA’s safe and precise motion solutions.
Block diagram of motorized cart with In-Wheel motors, driver, software, etc.
Customer challenges
- Motorized carts, drivetrain platforms and autonomous robots that carry heavy loads require precise control over inertia to avoid damage to carrying items and people
- Purchasing wheels, motors and gears separately increases the size of the product and require engineering resources to design ideal motion control
- In-Wheel motors are a solution to reduce the size of the product, but the space for housing circuit boards and a battery must also be considered
ASPINA solutions
- ASPINA offers compact In-Wheel motors integrated with brushless DC motor, planetary gears, wheel, and electromagnetic brake
- We can also develop circuit boards and software to drive and control the In-Wheel motor to provide precise and safe navigation, reduce the size of the customer's product and save customer's engineering resources
- Custom mechanical design of the In-Wheel motor and its related hardware fit into compact carts and robots
Exhibition information
-
May 19, 2025
-
Dec. 27, 2024
Related information
Contact us for more information
- New inquiry
- Prototype
- Upgrade
- Customization
- Your spec
- Literature
- Support
- Others